YALE Pallet Lift Truck Fault Codes DTC
Error: no LEDs or LCDs on
What the issue is: Inoperative
Cause of Problem: B+ and / or B- missing at controller, defective battery charger, or defective battery charger
What to do: Ensure the battery is connected, the key switch is on, and the brake override circuit is in the run position; also test your battery charger and motor controller and replace any
nonworking parts
Error: no LEDs or LCDs on
What the issue is: Forklift functions as normal
Cause of Problem: open connection between display and controller, defective display, or defective LEDs
What to do: make sure harnesses are connected at MDI and connector B on controller; test the dash display by connecting a handset to it and testing for communication; test LEDs by disconnecting
them, connecting the handset, and testing the handset; replace any non-working parts
Error: no LEDs or LCDs on
What the issue is: Forklift functions as normal
Cause of Problem: Because this condition is similar to the last, it will take a handset to determine its cause. If the handset displays “NO COMMUNICATION,” the controller is defective.
What to do: replace controller
Error: no alarm
What the issue is: Traction and hydraulic functions not working
Cause of Problem: improper startup sequence by jack operator
What to do: check brake switch, accelerator, steer handle, and hydraulic inputs
Error: AL66
What the issue is: Hydraulic function not working
Cause of Problem: battery voltage is low or controller voltage calibration is incorrect
What to do: Charge or replace battery; otherwise, use handset to determine the voltage read by the controller and compare it to an actual voltmeter reading; replace controller if the two readings
differ by more than 1.5 volts
Error: AL99
What the issue is: Traction and hydraulic functions not working
Cause of Problem: incorrect battery selected, damaged battery, or damaged connection to batter
What to do: check that you have the right voltage for your truck, manually check the voltage of your battery, inspect it for any damage, and check its connecting crimps and cables for damage as
well
Error: AL01
What the issue is: Traction and hoist functions not working
Cause of Problem: control card throttle or lift/lower calibration is out of range; control card is damaged or defective
What to do: Use the tester function on a handset to see if either calibration is greater than 1 volt at neutral; replace control card if damaged or defective, which can be checked by seeing if
both “forward switch” and “backward switch” are on at the same time when testing
Error: AL01
What the issue is: Traction and hoist functions not working
Cause of Problem: incomplete connection between control card and controller; traction reversing switch not connected; damaged or defective tiller card
What to do: Check connections between control card and controller; use a handset to test for operation of traction reversing switch; replace control card if tiller card is damaged
Error: AL02
What the issue is: Traction and hydraulic functions not working
Cause of Problem: main contactor tips are welded closed or motor field circuit is broken
What to do: disconnect power leads at contactor and test for an open circuit; check connections between motor field and controller
Error: AL04
What the issue is: traction and hydraulic functions not working
Cause of Problem: damaged connection to lowering valve; damaged lowering coil or lowering valve cartridge
What to do: check electrical connection between valve coil and controller; check lowering valve coil for resistance, replace if not approximately 17.7 ohms; replace lowering valve cartridge if
necessary
Error: AL05
What the issue is: traction and hydraulic functions not working
Cause: damaged connection to brake or brake coil damaged
What to do: check connection between electric brake and controller; check brake coil for resistance in both directions and replace if not between 27.36 and 30.24 ohms
Error: AL06
What the issue is: Traction and hydraulic functions not working
Cause of Problem: Damaged connection to traction motor; traction motor armature resistance is too low; field wires are loose or damaged; motor field winding is shorted or too low.
What to Do: Check electrical connection between traction motor, field wires, and controller; check traction motor armature for shorts; check motor field resistance and correct if not between 0.5
and 1.5 ohms; check contactor coil for resistance of 52 ohms
Error: AL07
What the issue is: traction functions reduced below 14°F or above 167°F and not working above 194°F
Cause of Problem: controller temperature is too hot or cold; controller temperature is not calibrated correctly; controller sensor or controller itself is damaged
What to do: move truck to a warmer or cooler location; use a handset to check that controller temperature matches room temperature (if not, replace controller)
Error: AL8
What the issue is: traction and hydraulic functions not working
Cause of Problem: over current in driven component
What to do: check main harness for damaged connections to main contactor, brake, and electric valve coils; check contactor, brake, and electric valve coils for correct resistance (52 ohms for
contactor, between 27.36 and 30.24 ohms for brake coil, and 17.7 ohms for electric valve coils)
Error: AL10
What the issue is: Traction and hydraulic functions not working
Cause of Problem: controller is damaged; damaged wire connection; short circuit in harness; ground between motor windings and chassis; motor field winding is shorted to chassis; field current
driver circuit has failed; watchdog hardware circuit is damaged
What to do: Cycle key switch off and on and replace controller if problem not solved; check wire connections at contactor, pump motor, and traction motor; check main harness for shorts; check for
grounds or shorts between motor windings and chassis; check motor field resistance (should be about 1.5 ohms); measure voltage between F1 and B- and F2 and B- on field current driver (should be
half the voltage between B+ and B-)
Error: AL94
What the issue is: Traction and hydraulic functions not working for one minute.
Cause of Problem: No fault is occurring. The controller is installing hour meter memory from MDI display if controller has been replaced.
What to do: No solution necessary. Fork truck will operate as soon as data transfer is complete.
MR series
1,400kg / 1,600kg / 2,000kg / 2,500kg
• Complete AC infrastructure on drive, hoist and steering motors
• Standard and Premium touch screen display
• 180° and 360° steering at the touch of a button
• AccuTouch™ mini-lever module or joystick controls
• Vehicle Control Manager — VCM
• Dual CANbus wiring
Reach Truck
MR series
2
Ast = Wa + R + a = Wa +(( l6 + x)
2
+ (b12/2 — b13)
2
+ a
Truck Dimensions
4.7
h6
4.8
h6
4.2
h1
4.5
h4
4.3
h2
4.10
h8
4.4
h3
4.22
s
l
1.8
x
4.19
l1
4.20
l2
4.28
l4
4.37
l7
1.9
y
1.6
c
4.32
m2
4.31
m1
Q
4.1
a
b
230
550
371
e
R
l6
4.34.1/4.34.2
Ast
a
2
a
2
4.25
b5
4.21
b1
4.24
b3
4.26
b4
4.21
b2
4.26
b12
3.7
b11
4.35
Wa
3
MR14, MR16, MR16N — Mast details, 3 stage full free lift (1,400kg / 1,600kg)
MR20, MR25 — Mast details, 3 stage full free lift (2,000kg / 2,500kg)
MR16HD — Mast details, Heavy Duty 3 stage full free lift (1,600kg)
Lift (h3)
mm
Lift (h3)
mm
Lift (h3)
mm
5000
5250
5500
5750
6000
6250
6500
6750
7000
7250
7500
7750
8000
8250
8500
8750
9000
9250
9500
9750
10000
10250
10500
4650
4900
5150
5400
5650
5900
6150
6400
6650
6900
7150
7400
7650
7900
8150
7900
8150
8400
8650
8900
9150
9400
9650
9900
10150
10400
10650
10900
11150
1140 0
(1)
With load backrest h4 + 508mm.
(2)
All weights are: mast structures (weldment, cylinders, chain, pulley) + carriage + load backrest + oil. Excluded: forks, accessories.
(1)
With load backrest h4 + 443mm.
(2)
All weights are: mast structures (weldment, cylinders, chain, pulley) + carriage + load backrest + oil. Excluded: forks, accessories.
(1)
With load backrest h4 + 508mm.
(2)
All weights are: mast structures (weldment, cylinders, chain, pulley) + carriage + load backrest + oil. Excluded: forks, accessories.
1648
1734
1820
1906
1992
2078
2164
2250
2336
2422
2508
2594
2680
2766
2852
2938
3024
3110
3196
3282
3368
3454
3540
1582
1668
1754
1840
1926
2012
2098
2184
2270
2356
2442
2528
2614
2700
2786
2680
2766
2852
2938
3024
3110
3196
3282
3368
3454
3540
3626
3712
3798
3884
2195
2281
2367
2453
2539
2625
2711
2797
2883
2969
3055
3141
3227
3313
3399
3485
3571
3657
3743
3829
3915
4001
4087
2195
2281
2367
2453
2539
2625
2711
2797
2883
2969
3055
3141
3227
3313
3399
3227
3313
3399
3485
3571
3657
3743
3839
3925
4011
4097
4183
4269
4355
4441
5563
5813
6063
6313
6563
6813
7063
7313
7563
7813
8063
8313
8563
8813
9063
9313
9563
9813
10063
10313
10563
10813
11063
5263
5513
5763
6013
6263
6513
6763
7013
7263
7513
7763
8013
8263
8513
8763
8463
8713
8963
9213
9463
9713
9963
10213
10463
10713
10963
11213
11463
11713
11963
911
936
961
986
1010
1035
1060
1090
1115
1140
1164
1220
1244
1269
1299
1324
1349
1376
1400
1425
1454
1478
1503
958
985
1012
1038
1065
1092
1118
1150
1177
1204
1230
1288
1314
1341
1373
1376
1404
1438
1466
1495
1524
1552
1580
1612
1641
1699
1728
1756
1785
1813
Free lift (h2)
mm
Free lift (h2)
mm
Free lift (h2)
mm
Height of mast lowered (h1)
mm
Height of mast lowered (h1)
mm
Height of mast lowered (h1)
mm
Height of mast extended (h4)
mm
(1)
Height of mast extended (h4)
mm
(1)
Height of mast extended (h4)
mm
(1)
Wei gh t
kg
(2)
Wei gh t
kg
(2)
Wei gh t
kg
(2)
MR14, MR16
MR16N
MR20HD — Mast details, Heavy Duty 3 stage full free lift (2,000kg)
MR14 truck dimensions for batteries
MR16 truck dimensions for batteries
Lift (h3)
mm
7750
8000
8250
8500
8750
9000
9250
9500
9750
10000
10250
10500
10750
11000
11250
1150 0
11750
12000
12250
12500
(1)
With load backrest h4 + 443mm.
(2)
All weights are: mast structures (weldment, cylinders, chain, pulley) + carriage + load backrest + oil. Excluded: forks, accessories.
2614
2700
2786
2872
2958
3044
3130
3216
3302
3388
3474
3560
3646
3732
3818
3904
3990
4076
4162
4248
3227
3313
3399
3485
3571
3657
3743
3839
3925
4011
4097
4183
4269
4355
4441
4527
4613
4699
4785
4871
8363
8613
8863
9113
9363
9613
9863
10113
10363
10613
10863
11113
11363
11613
11863
12113
12363
12613
12863
13113
1402
1431
1465
1494
1523
1552
1581
1609
1638
1671
1729
1758
1787
1816
1844
1873
1902
1931
1959
1988
Free lift (h2)
mm
Height of mast lowered (h1)
mm
Height of mast extended (h4)
mm
(1)
Wei gh t
kg
(2)
Battery type
Manufacturer’s type designation
Load distance, centre of drive axle to fork
Wheelbase
Service weight
Axle loading, unladen front/rear
(5)
Axle loading fork advanced, laden front/rear
Axle loading fork retracted, laden front/rear
Overall length
Length to face of forks
Reach distance
Aisle width for pallets 1000mm x 1200mm crossways
Aisle width for pallets 800mm x 1200mm lengthways
Turning radius
Battery according to DIN 43531/35/36 A, B, C, no
Battery voltage/nominal capacity K5
Battery weight
(4)
Battery type
Manufacturer’s type designation
Load distance, centre of drive axle to fork
Wheelbase
Service weight
Axle loading, unladen front/rear
(5)
Axle loading fork advanced, laden front/rear
Axle loading fork retracted, laden front/rear
Overall length
Length to face of forks
Reach distance
Aisle width for pallets 1000mm x 1200mm crossways
Aisle width for pallets 800mm x 1200mm lengthways
Turning radius
Battery according to DIN 43531/35/36 A, B, C, no
Battery voltage/nominal capacity K5
Battery weight
(4)
x (mm)
y (mm)
kg
kg
kg
kg
l1 (mm)
l2 (mm)
l4 (mm)
Ast (mm)
Ast (mm)
Wa (mm)
(V) / (Ah)
kg
x (mm)
y (mm)
kg
kg
kg
kg
l1 (mm)
l2 (mm)
l4 (mm)
Ast (mm)
Ast (mm)
Wa (mm)
(V) / (Ah)
kg
C “Super”
MR14
452
1450
3162
2018 / 1144
601 / 4162
1853 / 2909
2379
1229
635
2731
2767
1718
C “Super”
48 / 465
750
C “Super”
MR16
452
1450
3162
2018 / 1144
601 / 4162
1853 / 2909
2379
1229
635
2731
2767
1718
C “Super”
48 / 465
750
C
MR14
380
1450
3360
2069 / 1291
714 / 4246
1825 / 3135
2451
1301
563
2781
2830
1718
C
48 / 560
939
C
MR16
380
1450
3360
2069 / 1291
714 / 4246
1825 / 3135
2451
1301
563
2781
2830
1718
C
48 / 560
939
C “Super”
MR14
380
1450
3371
2077 / 1294
721 / 4250
1832 / 3139
2451
1301
563
2781
2830
1718
C “Super”
48 / 620
950
C “Super”
MR16
380
1450
3371
2077 / 1294
721 / 4250
1832 / 3139
2451
1301
563
2781
2830
1718
C “Super”
48 / 620
950
C
MR14
308
1450
3546
2103 / 1443
810 / 4336
1779 / 3367
2523
1373
491
2834
2896
1718
C
48 / 700
1119
C
MR16
308
1450
3546
2103 / 1443
810 / 4336
1779 / 3367
2523
1373
491
2834
2896
1718
C
48 / 700
1119
C “Super”
MR14
308
1450
3592
2133 / 1459
839 / 4352
1809 / 3383
2523
1373
491
2834
2896
1718
C “Super”
48 / 775
1165
C “Super”
MR16
308
1450
3592
2133 / 1459
839 / 4352
1809 / 3383
2523
1373
491
2834
2896
1718
C “Super”
48 / 775
1165
1.2
1.8
1.9
2.1
2.3
2.4
2.5
4.19
4.20
4.28
4.34.1
4.34.2
4.35
6.3
6.4
6.5
1.2
1.8
1.9
2.1
2.3
2.4
2.5
4.19
4.20
4.28
4.34.1
4.34.2
4.35
6.3
6.4
6.5
Distinguishing
mark
Distinguishing
mark
Weights
Weights
Dimensions
Dimensions
Eletric-
engine
Eletric-
engine
MR series
4
MR16N truck dimensions for batteries
MR20 truck dimensions for batteries
MR25 truck dimensions for batteries
Battery type
Manufacturer’s type designation
Load distance, centre of drive axle to fork
Wheelbase
Service weight
Axle loading, unladen front/rear
(5)
Axle loading fork advanced, laden front/rear
Axle loading fork retracted, laden front/rear
Overall length
Length to face of forks
Reach distance
Aisle width for pallets 1000mm x 1200mm crossways
Aisle width for pallets 800mm x 1200mm lengthways
Turning radius
Battery according to DIN 43531/35/36 A, B, C, no
Battery voltage/nominal capacity K5
Battery weight
(4)
x (mm)
y (mm)
kg
kg
kg
kg
l1 (mm)
l2 (mm)
l4 (mm)
Ast (mm)
Ast (mm)
Wa (mm)
(V) / (Ah)
kg
B “Super”
MR16N
382
1450
3115
1924 / 1191
572 / 4143
1682 / 3033
2449
1299
565
2762
2811
1700
B “Super”
48 / 465
750
B
MR16N
292
1450
3309
1947 / 1362
672 / 4237
1606 / 3303
2539
1389
475
2828
2893
1700
B
48 / 560
937
B “Super”
MR16N
292
1450
3317
1952 / 1365
677 / 4240
1611 / 3306
2539
1389
475
2828
2893
1700
B “Super”
48 / 620
945
B
MR16N
202
1450
3498
1955 / 1543
757 / 4341
1514 / 3584
2629
1479
385
2898
2976
1700
B
48 / 700
1119
B “Super”
MR16N
202
1450
3514
1965 / 1549
766 / 4347
1524 / 3590
2629
1479
385
2899
2976
1700
B “Super”
48 / 775
1135
1.2
1.8
1.9
2.1
2.3
2.4
2.5
4.19
4.20
4.28
4.34.1
4.34.2
4.35
6.3
6.4
6.5
Distinguishing
mark
Distinguishing
mark
Distinguishing
mark
Weights
Weights Weights
Dimensions
Dimensions Dimensions
Eletric-
engine
Eletric-
engine
Eletric-
engine
5
C “Super”
MR20
430
1500
3626
2268 / 1358
679 / 4947
2039 / 3586
2451
1301
613
2795
2835
1767
C “Super”
48 / 620
950
C “Super”
MR25
503
1650
4084
2552 / 1532
804 / 5780
2402 / 4182
2528
1378
686
2890
2915
1911
C “Super”
48 / 775
1165
C
MR20
358
1500
3801
2296 / 1504
770 / 5030
1971 / 3829
2523
1373
541
2846
2900
1767
C
48 / 700
1119
C
MR25
431
1650
4230
2565 / 1665
876 / 5855
2306 / 4424
2600
1450
614
2938
2978
1911
C
48 / 840
1306
C “Super”
MR20
358
1500
3847
2326 / 1520
801 / 5046
2002 / 3845
2523
1373
541
2846
2900
1767
C “Super”
48 / 775
1165
C “Super”
MR25
431
1650
4292
2606 / 1686
917 / 5875
2348 / 4444
2600
1450
614
2938
2978
1911
C “Super”
48 / 930
1368
Battery type
Manufacturer’s type designation
Load distance, centre of drive axle to fork
Wheelbase
Service weight
Axle loading, unladen front/rear
(5)
Axle loading fork advanced, laden front/rear
Axle loading fork retracted, laden front/rear
Overall length
Length to face of forks
Reach distance
Aisle width for pallets 1000mm x 1200mm crossways
Aisle width for pallets 800mm x 1200mm lengthways
Turning radius
Battery according to DIN 43531/35/36 A, B, C, no
Battery voltage/nominal capacity K5
Battery weight
(4)
x (mm)
y (mm)
kg
kg
kg
kg
l1 (mm)
l2 (mm)
l4 (mm)
Ast (mm)
Ast (mm)
Wa (mm)
(V) / (Ah)
kg
Battery type
Manufacturer’s type designation
Load distance, centre of drive axle to fork
Wheelbase
Service weight
Axle loading, unladen front/rear
(5)
Axle loading fork advanced, laden front/rear
Axle loading fork retracted, laden front/rear
Overall length
Length to face of forks
Reach distance
Aisle width for pallets 1000mm x 1200mm crossways
Aisle width for pallets 800mm x 1200mm lengthways
Turning radius
Battery according to DIN 43531/35/36 A, B, C, no
Battery voltage/nominal capacity K5
Battery weight
(4)
x (mm)
y (mm)
kg
kg
kg
kg
l1 (mm)
l2 (mm)
l4 (mm)
Ast (mm)
Ast (mm)
Wa (mm)
(V) / (Ah)
kg
1.2
1.8
1.9
2.1
2.3
2.4
2.5
4.19
4.20
4.28
4.34.1
4.34.2
4.35
6.3
6.4
6.5
1.2
1.8
1.9
2.1
2.3
2.4
2.5
4.19
4.20
4.28
4.34.1
4.34.2
4.35
6.3
6.4
6.5
MR16HD truck dimensions for batteries
MR20HD truck dimensions for batteries
Standard equipment and options
Distinguishing
mark
Distinguishing
mark
Weights Weights Dimensions Dimensions
Operator Compartment
Eletric-
engine
Eletric-
engine
C “Super”
MR16HD
308
1450
4049
2424 / 1625
891 / 4758
2180 / 3469
2523
1373
491
2834
2896
1718
C “Super”
48 / 620
950
C “Super”
MR20HD
353
1500
4471
2597 / 1874
921 / 5550
2266 / 4205
2528
1378
536
2850
2904
1767
C “Super”
48 / 775
1165
C
MR16HD
308
1450
4224
2428 / 1796
979 / 4845
2104 / 3720
2523
1373
491
2834
2896
1718
C
48 / 700
1119
C
MR20HD
281
1500
4617
2577 / 2040
985 / 5632
2149 / 4468
2600
1450
464
2903
2970
1767
C
48 / 840
1306
C “Super”
MR16HD
308
1450
4270
2457 / 1813
1009 / 4861
2134 / 3736
2523
1373
491
2834
2896
1718
C “Super”
48 / 775
1165
C “Super”
MR20HD
281
1500
4679
2616 / 2063
1024 / 5655
2189 / 4490
2600
1450
464
2903
2970
1767
C “Super”
48 / 930
1368
Battery type
Manufacturer’s type designation
Load distance, centre of drive axle to fork
Wheelbase
Service weight
Axle loading, unladen front/rear
(5)
Axle loading fork advanced, laden front/rear
Axle loading fork retracted, laden front/rear
Overall length
Length to face of forks
Reach distance
Aisle width for pallets 1000mm x 1200mm crossways
Aisle width for pallets 800mm x 1200mm lengthways
Turning radius
Battery according to DIN 43531/35/36 A, B, C, no
Battery voltage/nominal capacity K5
Battery weight
(4)
x (mm)
y (mm)
kg
kg
kg
kg
l1 (mm)
l2 (mm)
l4 (mm)
Ast (mm)
Ast (mm)
Wa (mm)
(V) / (Ah)
kg
Battery type
Manufacturer’s type designation
Load distance, centre of drive axle to fork
Wheelbase
Service weight
Axle loading, unladen front/rear
(5)
Axle loading fork advanced, laden front/rear
Axle loading fork retracted, laden front/rear
Overall length
Length to face of forks
Reach distance
Aisle width for pallets 1000mm x 1200mm crossways
Aisle width for pallets 800mm x 1200mm lengthways
Turning radius
Battery according to DIN 43531/35/36 A, B, C, no
Battery voltage/nominal capacity K5
Battery weight
(4)
Notes — relates to all battery dimensions tables.
(4)
These values may vary of +/- 5%.
(5)
Forks retracted. All weights (2.1 to 2.5) are with lowest mast and standard forks.
x (mm)
y (mm)
kg
kg
kg
kg
l1 (mm)
l2 (mm)
l4 (mm)
Ast (mm)
Ast (mm)
Wa (mm)
(V) / (Ah)
kg
1.2
1.8
1.9
2.1
2.3
2.4
2.5
4.19
4.20
4.28
4.34.1
4.34.2
4.35
6.3
6.4
6.5
1.2
1.8
1.9
2.1
2.3
2.4
2.5
4.19
4.20
4.28
4.34.1
4.34.2
4.35
6.3
6.4
6.5
Feature
Intermediate step
Grab handle on overhead guard post
Grab handle under armrest
AccuTouch™ mini-levers mounted on adjustable length armrest
Joystick mounted on adjustable length armrest
Full suspension seat — 60 mm suspension travel cloth upholstery
Full suspension seat — 80 mm suspension travel cloth upholstery
Headrest (cloth version only)
Synchronised seat cushion and backrest movement (cloth version only)
Seat belt
Heated seat
Antistatic seat (cloth version only)
Vinyl seat upholstery
Standard display
Premium display with touch screen
Keyless access
Adjustable steering column
Automatic park brake Yalestop
180° steering
360° steering
Driver select steering mode 180/360° (push button)
MR14 / 16 MR16N MR20 / 25 MR16HD MR20HD
n n n n n
n n n n n
n n n n n
n n n n n
m m m m m
n n n n n
m m m m m
m m m m m
m m m m m
m m m m m
m m m m m
m m m m m
m m m m m
n n n n n
m m m m m
m m m m m
n n n n n
n n n n n
n n n n n
m m m m m
m m m m m
MR series
6
Standard equipment and options (continued)
Travel performance
Lift performance / driver assistApplication environmentChassis / Battery sizes
Feature
Travel speed 11 km/h
Travel speed 14 km/h with electric load wheel braking
Speed slow down mast reached forward
Speed slow down on cornering
Speed slow down over free lift
3 stage mast / tilting carriage
Simultaneous lift / reach functionality
Simultaneous hydraulic functionality — 3 functions
Mast cushioning over free lift/main lift sections — fixed sensor mounting
Lift Comfort package (1)
Lift Performance package
Laser line fork positioning aid (above free lift)
Auto side shift centring
Auto fork levelling in the horizontal position
Height preselector (with/without pallet detection device)
Fork mounted camera / monitor
Weight indicator
5th hydraulic function
Universal support bracket
Beverage holder and document tray
A4 clipboard
Stretch film roll holder
Lift limit with override (1 x height setting )
Lift limit with override (2 x height settings)
Lower limit (with override option)
Flashing beacon
Work lights x 2 (mast side)
Work lights x 2 (drive side)
Polycarbonate (lexan) protection on overhead guard
Metal grid protection on overhead guard
Top / front load wheel protection
Side load wheel protection
High temperature environment
Side battery change — battery tray rollers
Side battery change table
Extension cable
Drive-in overhead guard (w900 x h1400 / w900 x h1700 mm)
Antistatic drive and load wheels
Wet surface drive and load wheels
Side guidance rollers
DC/DC converter (choice of 12V/48V, 24V / 48V, 12-24V / 48V options)
Audible alarm (choice of forks leading, forks trailing, both travel directions)
Load backrest (choice of heights 1000 / 1500 mm)
Chassis width (max) 1265 mm
1125 mm
1345 mm
Battery sizes
(2)
420 — 465 Ah
560 — 620 Ah
700 — 775 Ah
840 — 930 Ah
MR14 / 16 MR16N MR20 / 25 MR16HD MR20HD
n n B B B
m m n n n
n n n n n
n n n n n
n n n n n
n n n n n
n n n n n
m m m m m
n n n n B
m m m n n
m m B n n
m m m m m
m m m m m
m m m m m
m m m m m
m m m m m
m m m m m
m m m m m
m m m m m
m m m m m
m m m m m
m m m m m
m m m m m
m m m m m
m m m m m
m m m m m
m m m m m
m m m m m
m m m m m
m m m m m
n n n n n
m m m m m
m m m m m
m m m m m
m m m m m
m m m m m
m m m m m
m m m m m
m m m m m
m m MR20 m m
m m m m m
m m m m m
m m m m m
n B MR20 n B
B n B B B
B B MR25 B m
m m B B B
m m mMR20 m B
m m m m m
B B mMR25 B m
7
(1)
Includes;
End of stroke slow down on lift.
Soft stop on lowering.
Height controlled mast cushioning over Free Lift/Main lift mast section.
Height indicator.
(2)
DIN C battery on MR14/MR16/MR20/MR25/MR16HD/MR20HD
DIN B battery on MR16N
n Standard
m Optional
B Not available
MR14, MR16, MR16N, MR16HD, MR20, MR20HD, MR25 — General Specifications
Distinguishing markWeightsTyres/chassisDimensions Performance data Electric-engine
Addition data
(1)
With load backrest h4 + 508mm MR14-MR16-MR16N-MR16HD,
+ 443mm MR20-MR25-MR20HD.
(2)
With beacon h6 + 120mm. ; With OHG Grid Protector h6 + 20mm
; With OHG Screen Protector h6 + 30mm.
(3)
With load wheels lateral covers: 1289mm MR14-MR16-
MR20-MR16HD, 1153mm (MR16N), 1373mm (MR25-MR20HD).
(4)
These values may vary of +/- 5%.
(5)
Forks retracted.
(6)
See Truck dimensions for batteries tables.
1.1
1.2
1.3
1.4
1.5
1.6
1.8
1.9
2.1
2.3
2.4
2.5
3.1
3.2
3.3
3.5
3.7
4.1
4.2
4.3
4.4
4.5
4.7
4.8
4.10
4.19
4.20
4.21
4.22
4.23
4.24
4.25
4.26
4.28
4.31
4.32
4.34.1
4.34.2
4.35
4.37
4.43
5.1
5.1.1
5.2
5.3
5.4
5.7
5.8
5.9
5.10
6.1
6.2
6.3
6.4
6.5
6.6
8.1
10.1
10.2
10.7
Manufacturer (abbreviation)
Manufacturer’s type designation
Drive: electric (battery or mains), diesel, petrol, fuel gas
Operator type: hand, pedestrian, standing, seated, order-picker
Rated capacity/rated load
Load centre distance
Load distance, centre of drive axle to fork
Wheelbase
Service weight
Axle loading, laden front/rear
(5)
Axle loading, fork advanced, laden front/rear
Axle loading, fork retracted, unladen front/rear
Tyres: polyurethane, topthane, vulkollan, front/rear
Tyre size, front
Tyre size, rear
Wheels, number front/rear (x = driven wheels)
Tread, rear
Tilt of mast/fork carriage forward/backward β
Height of mast, lowered
Free lift
Lift
Height, mast extended
(1)
Height of overhead guard (cabin)
(2)
Seat height/stand height
Height of wheel arms
Overall length
Length to face of forks
Overall width
(3)
Fork dimensions ISO2331
Fork carriage ISO 2328, class/type A,B
Fork carriage width
Distance between fork-arms, min./max.
(8)
Distance between wheel arms / loading surfaces
Reach distance
Ground clearance, laden, below mast
Ground clearance, centre of wheelbase
Aisle width for pallets 1000mm x 1200mm crossways
Aisle width for pallets 800mm x 1200mm lengthways
Turning radius
Length across load arms
Step height
Travel speed, laden/unladen
(7)
Travel speed, laden/unladen, backwards
(7)
Lift speed, laden/unladen
Lowering speed, laden/unladen
Reaching speed, laden/unladen
Gradeability laden/unladen
Max gradeability laden/unladen
Acceleration time laden/unladen
Service brake
Drive motor rating S2 60 min
Lift motor rating at S3 15%
Battery according to DIN 43531/35/36 A, B, C, no
Battery voltage/nominal capacity K5
Battery weight
(4)
Energy consumption according to VDI cycle
Type of drive unit
Operating pressure for attachments
Oil volume for attachments
Sound pressure level at the driver’s seat
Q (kg)
c (mm)
x (mm)
y (mm)
kg
kg
kg
kg
ø mm x mm
ø mm x mm
b11 (mm)
β / β (°)
h1 (mm)
h2 (mm)
h3 (mm)
h4 (mm)
h6 (mm)
h7 (mm)
h8 (mm)
l1 (mm)
l2 (mm)
b1/b2 (mm)
s/e/l (mm)
b3 (mm)
b5 (mm)
b4 (mm)
l4 (mm)
m1 (mm)
m2 (mm)
Ast (mm)
Ast (mm)
Wa (mm)
l7 (mm)
mm
km/h
km/h
m/s
m/s
m/s
%
%
s
kW
kW
(V) / (Ah)
kg
kWh/h @ Nr of Cycles
bar
l/min
dB (A)
Yale
MR14
Electric (Battery)
Seated
1400
600
402
1400
3112
1977 / 1135
682 / 3830
1778 / 2735
Vulkollan / Vulkollan
343 x 140
285 x 100
1 x /2
1155
2 / 4
2195
1648
5000
5563
2175
1082
308
2379
1229
1265
40 / 80 / 1150
2A
700
220 / 640
900
585
75
75
2718
2764
1671
1795
371
11 / 11 (14 / 14)
11 / 11 (14 / 14)
0.37 / 0.63 (0.47 / 0.73)
0.55 / 0.55
0.15 / 0.15
12 / 15
12 / 15
on request
Electric
6.4
14
C
48 / 420
(6)
750
on request
AC
180
20
<69.7
Yale
MR16
Electric (Battery)
Seated
1600
600
452
1450
3162
2018 / 1144
601 / 4162
1853 / 2909
Vulkollan / Vulkollan
343 x 140
285 x 100
1 x /2
1155
2 / 4
2195
1648
5000
5563
2175
1082
308
2379
1229
1265
40 / 120 / 1150
2A
700
260 / 680
900
635
75
75
2731
2767
1718
1845
371
11 / 11 (14 / 14)
11 / 11 (14 / 14)
0.32 / 0.63 (0.42 / 0.73)
0.55 / 0.55
0.15 / 0.15
11 / 15
12 / 15
on request
Electric
6.4
14
C
48 / 420
(6)
750
on request
AC
180
20
<69.7
MR series
8
MR14, MR16, MR16N, MR16HD, MR20, MR20HD, MR25 — General Specifications
Distinguishing markWeightsTyres/chassisDimensions Performance data Electric-engine
Addition data
(7)
Values in brackets are Optional.
(8)
Sideshift distance on either side is + / -75 mm on
all trucks. Reduction of + / — 25 mm on MR16N.
All values are nominal values and they are subject to tolerances.
For further information, please contact the manufacturer.
Yale products might be subject to change without notice.
Lift trucks illustrated may feature optional equipment.
Values may vary with alternative configurations.
1.1
1.2
1.3
1.4
1.5
1.6
1.8
1.9
2.1
2.3
2.4
2.5
3.1
3.2
3.3
3.5
3.7
4.1
4.2
4.3
4.4
4.5
4.7
4.8
4.10
4.19
4.20
4.21
4.22
4.23
4.24
4.25
4.26
4.28
4.31
4.32
4.34.1
4.34.2
4.35
4.37
4.43
5.1
5.1.1
5.2
5.3
5.4
5.7
5.8
5.9
5.10
6.1
6.2
6.3
6.4
6.5
6.6
8.1
10.1
10.2
10.7
Yale
MR16N
Electric (Battery)
Seated
1600
600
382
1450
3111
1922 / 1189
569 / 4142
1680 / 3032
Vulkollan / Vulkollan
343 x 140
285 x 100
1 x /2
1025
2 / 4
2195
1648
5000
5563
2175
1082
308
2449
1299
1125
40 / 120 / 1150
2A
700
260 / 680
795
565
75
75
2762
2811
1700
1845
371
11 / 11 (14 / 14)
11 / 11 (14 / 14)
0.32 / 0.63 (0.42 / 0.73)
0.55 / 0.55
0.15 / 0.15
11 / 15
12 / 15
on request
Electric
6.4
14
C
48 / 420
(6)
750
on request
AC
180
20
<69.7
Yale
MR16HD
Electric (Battery)
Seated
1600
600
308
1450
4038
2417 / 1621
883 / 4755
2172 / 3466
Vulkollan / Vulkollan
343 x 140
285 x 100
1x/2
1155
2 / 4
3227
2680
8050
8613
2175
1082
308
2523
1373
1265
40 / 120 / 1150
2A
700
260/680
900
491
65
65
2834
2896
1718
1845
371
14 / 14
14 / 14
0.42 / 0.73
0.55 / 0.55
0.15 / 0.15
10 / 14
12 / 15
on request
Electric
6.4
14
C
48 / 700
(6)
939
on request
AC
180
20
<69.7
Yale
MR20
Electric (Battery)
Seated
2000
600
430
1500
3615
2261 / 1354
671 / 4943
2032 / 3583
Vulkollan / Vulkollan
343 x 140
285 x 100
1x/2
1155
2 / 4
2195
1582
4650
5263
2175
1082
308
2451
1301
1265
40 / 120 / 1150
2A
700
260/680
900
613
65
65
2795
2835
1767
1895
371
14 / 14
14 / 14
0.37 / 0.64
0.55 / 0.50
0.15 / 0.15
10 / 15
12 / 15
on request
Electric
6.4
14
C
48 / 560
(6)
939
on request
AC
180
20
<69.7
Yale
MR20HD
Electric (Battery)
Seated
2000
600
353
1500
4425
2567 / 1858
891 / 5534
2235 / 4189
Vulkollan / Vulkollan
343 x 140
285 x 140
1x/2
1195
2 / 4
3227
2614
7900
8513
2175
1082
308
2528
1378
1345
45 / 120 / 1150
2A
700
260/680
900
536
65
65
2850
2904
1767
1895
371
14 / 14
14 / 14
0.37 / 0.68
0.55 / 0.55
0.15 / 0.15
8 / 13
12 / 15
on request
Electric
6.4
14
C
48 / 700
(6)
1119
on request
AC
180
20
<69.7
Yale
MR25
Electric (Battery)
Seated
2500
600
503
1650
4038
2520 / 1518
773 / 5765
2371 / 4167
Vulkollan / Vulkollan
343 x 140
285 x 140
1x/2
1195
2 / 4
2195
1582
4650
5263
2175
1082
308
2528
1378
1345
45 / 120 / 1150
2A
700
260/680
900
686
65
65
2890
2915
1911
2045
371
14 / 14
14 / 14
0.30 / 0.64
0.55 / 0.50
0.15 / 0.15
8 / 14
12 / 15
on request
Electric
6.4
14
C
48 / 700
(6)
1119
on request
AC
180
20
<69.7
9
MR series
Models: MR14, MR16, MR16N, MR16HD, MR20, MR20HD, MR25
MR series
10
The new Yale®MR Series Reach Truck
features three piece design same for all
different models. The main
differentiators between the models are
the wheelbase and the truck width.
Overhead Guard
The one piece welded overhead guard
gives a good visibility to all directions.
The two different pillar profiles give
adequate stiffness strength, with a
minimum impact on visibility. As option
drive-in overhead guards are available.
Operator compartment
The operator compartment structure is
a one piece welded structure
developed for long term durability. It is
bolted on the frame having boxed
bottom part for stiff compartment and
reduced vibrations to the operator.
The step with grip profile has a
maximum depth of 130 mm and low
height of 371mm.
Frame
Completely welded base frame is
available in 2 basic widths and 4
different lengths. The HD version has
an increased width over the load arms.
The width is reduced to the standard
width of the frame with an angled plate
at the connection to the load arms and
rear frame.
Seats
Two different full-suspension seats with
additional options are available, both of
which are adjustable for operator
weight, fore/aft position and backrest
angle.
Steering console
The steering console is one hand
adjustable for length to provide the
optimum position for the operator. It
has a 10° incline in the direction of the
operator, as a result of the length
adjustment the height will increase with
17.5 mm from the max in to max out
position. This will ease the in- and
egress of the operator even in
extracted steering column position. To
improve operators left arm ergonomics
the steering column is slightly 3°
angled anti clockwise.
Steering system
The steering system is a fully fly-by-
wire system. The steer wheel input and
the steer motor output are connected
to the controller and managed by the
VCM. The steer positioning sensors
provide feedback of the actual steer
position. The standard steering has a
180° steer angle, a 360° option is
available and enabled by the VCM
software. A third option allows
switching from 180° to 360° by
pressing a steering mode selection
switch on the dashboard. Speed
reduction on cornering is automatic
and can be adjusted.
Foot pedals
Low resistant foot pedals positioned on
the slightly inclined (13°) floor plate to
improve the pedal operation
ergonomics. The useful operator floor
space is increased with the pedal
layout is divided over the available
width. The operator presence switch is
slightly rotated to the mid line off the
operator seat to improve operator left
11
foot position. The thick (min. 8 mm) one
piece floor mat absorbs vibrations and
noise out of the motor compartment.
Dash display
The display is integrated in the
dashboard in front of the operator. In
this location the display is easy to read
and to operate. The standard display
utilises the proven display design from
Yale ECB trucks. An optional industry
first premium touch screen display
allows operators to be in full control of
the truck at all times.
Vehicle Control Manager
The Vehicle Control Manager (VCM) is
the central module of the truck and it is
linked to the truck modules via Dual
CANbus system to increase reliability
and truck dependability. With this
proven technology used in the
automobile sector point to point wiring
is greatly reduced.
Hydraulic controls
The Hydraulic controls are integrated in
ergonomic sliding armrest under
driver’s right hand. The standard
controls is proven AccuTouch™
mini-levers module with separate horn
and direction switches. New designed
Joystick with integrated mini lever
joystick for best ergonomic hydraulic
operation is available as option.
Masts
New 3 stage full free lift mast
incorporates new unique Yale designed
profiles that reduce the total mast
channel width. Lift cylinders position
optimised to increase operator visibility
and cross members are not in direct
line of visibility for critical heights. The
stiff and robust mast carriage is a
welded construction made out of two
lateral plates of 30 mm and several
cross bars and base plate of 12 mm
thick to create an open boxed frame.
Motors
The next generation AC drive motor is
standard across the model range. The
drive motor remains in a fixed position
to avoid flexing of the power cables.
Optimised acceleration and travel
speed performance (up to 14 km/h)
delivers high load handling efficiency
productivity. Easy access through
swing-open motor compartment door.
The steering motor also uses AC
technology and the gear on gear
arrangement provides a positive mesh
for precise steering control. On power
up the drive wheel is automatically
centred. A removable plate allows
access to the drive tyre/ gear reducer
for servicing. The motor compartment
including the hoist motor is ventilated.
MR series
Models: MR14, MR16, MR16N, MR16HD,
MR20, MR20HD, MR25
HYSTER-YALE UK LIMITED
trading as Yale Europe Materials Handling
Centennial House,
Frimley Business Park,
Frimley, Surrey GU16 7SG, United Kingdom.
Tel: +44 (0) 1276 538500 Fax: +44 (0) 1276 538559
www.yale-forklifts.eu
Publication part no. 220990209 Rev.12 Printed in The Netherlands (0116HG) EN.
Safety: This truck conforms to the current EU requirements. Specification is subject to change
without notice.
Yale, VERACITOR and are registered trademarks. “PEOPLE, PRODUCTS, PRODUCTIVITY”,
PREMIER, Hi-Vis, and CSS are trademarks in the United States and certain other jurisdictions.
MATERIALS HANDLING CENTRAL and MATERIAL HANDLING CENTRAL are Service Marks
in the United States and certain other jurisdictions. is a Registered Copyright.
© Yale Europe Materials Handling 2016. All rights reserved.
Truck shown with optional equipment. Country of Registration: England and Wales.
Company Registration Number: 02636775
Skip to content
Yale and Hyster Forklift Error Codes List
How to clear fault codes Yale and Hyster forklift
Here are the most popular error codes for the Hyster and Yale forklifts to find the diagnostic and possible cases.
On Yale and Hyster forklift fault code can be showed or can be in the system.
In order to troubleshoot, diagnose, and also possible cases error codes, you can look for your error code and all useful description in the table below
if you have any questions you can leave the question here Forklift Error codes and our technicians can help you
Fault Codes | Diagnostic Codes | Possible Cases |
---|---|---|
524223-0 | XMSN Reverse Pressure Greater Than Commanded Pressure | A. SENSOR SUPPLY OPEN CIRCUIT B. SENSOR FAILURE C. FUNCTIONAL FAILURE — MECHANICAL D. FUNCTIONAL FAILURE IN CONTROLLER |
524225-0 | XMSN Forward Pressure Greater Than Commanded Pressure | |
524223-1 | XMSN Reverse Pressure Less Than Commanded | A. LOW TRANSMISSION OIL LEVEL B. SENSOR SUPPLY OPEN CIRCUIT C. SENSOR FAILURE D. FUNCTIONAL FAILURE — MECHANICAL E. FUNCTIONAL FAILURE IN CONTROLLER |
524225-1 | XMSN Forward Pressure Less Than Commanded | |
105-3 | Intake Air Temperature (IAT) Sensor OORH | A. SENSOR WIRING OPEN CIRCUIT B. SENSOR SIGNAL SHORTED TO 5V OR BATTERY VOLTAGE C. SENSOR FAILURE D. FUNCTIONAL FAILURE IN CONTROLLER |
110-3 | Coolant Temperature Sensor OORH | |
177-3 | Transmission Oil Temperature Sensor OORH | |
522603-3 | Fuel Temp (LPG) Sensor OORH | |
105-4 | Intake Air Temperature (IAT) Sensor OORL | A. SENSOR SIGNAL SHORTED TO SENSOR GROUND. B. SENSOR SIGNAL SHORTED TO FRAME GROUND. C. SENSOR FAILURE D. FUNCTIONAL FAILURE IN CONTROLLER |
110-4 | Coolant Temperature Sensor OORL | |
177-4 | Transmission Oil Temperature Sensor OORL | |
522603-4 | Fuel Temp (LPG) Sensor OORL | |
522712-3 | Accelerator A Position Sensor OORH | A. SENSOR SUPPLY OPEN CIRCUIT (SENSOR SIGNAL GROUNDS) B. B SENSOR SIGNAL OPEN CIRCUIT C. SENSOR SIGNAL SHORTED TO BATTERY SOURCE D. SENSOR SIGNAL SHORTED TO SENSOR SUPPLY |
522713-3 | Accelerator B Position Sensor OORH | |
522712-4 | Accelerator A Position Sensor OORL | A. SENSOR SUPPLY OPEN CIRCUIT (+5 VOLTS) B. SENSOR SIGNAL A OPEN CIRCUIT C. SENSOR SIGNAL SHORTED TO FRAME GROUND D. SENSOR SIGNAL SHORTED TO SENSOR GROUND E. SENSOR FAILURE F. FUNCTIONAL FAILURE IN CONTROLLER |
522713-4 | Accelerator B Position Sensor OORL | |
1079-31 | 5VE1 & 5VE2 Simultaneously OORH | A. ELECTRONIC THROTTLE ASSEMBLY (ETA) STICKY B. SENSOR (ETA) FAILURE C. FUNCTIONAL FAILURE IN CONTROLLER |
51-2 | Throttle Position Sensor Signals A and B Not Tracking Correctly | |
51-7 | Throttle Position Sensor Signals A and B Not At Commanded Value | |
51-31 | Throttle Position Sensor 1 & 2 Out of Range | |
2350-3 | DTC 2350-3 — Front Work Lights Relay (RL4) Driver Output OORH | A. SAFETY SWITCH (IF EQUIPPED) IS DISCONNECTED B. SHORT ON RELAY DRIVER OUTPUT TO UNSWITCHED BATTERY (SEEWARNING BEFORE CONTINUING) C. SHORT ON RELAY DRIVER OUTPUT TO SWITCHED BATTERY. D. SHORT ON RELAY DRIVER OUTPUT TO ANOTHER OPERATED DEVICE E. CONTROLLER DRIVER OUTPUT TO RELAY COIL OPEN CIRCUIT F. RELAY COIL OR GROUND CONNECTION OPEN CIRCUIT G. FUNCTIONAL FAILURE IN CONTROLLER |
522710-3 | Throttle A Position Sensor OORH | A. SENSOR GROUND OPEN CIRCUIT B. SENSOR SIGNAL SHORTED TO SENSOR SUPPLY C. SENSOR SIGNAL SHORTED TO BATTERY SOURCE D. SENSOR FAILURE E. FUNCTIONAL FAILURE IN CONTROLLER |
522711-3 | Throttle B Position Sensor OORH | |
522710-4 | Throttle A Position Sensor OORL | A. SENSOR SIGNAL OPEN CIRCUIT B. SENSOR SUPPLY OPEN CIRCUIT C. SENSOR SIGNAL SHORTED TO FRAME GROUND D. SENSOR SIGNAL SHORTED TO SENSOR GROUND E. SENSOR FAILURE F. FUNCTIONAL FAILURE IN CONTROLLER |
522711-4 | Throttle B Position Sensor OORL | |
521-3 | Brake Pedal Position Sensor OORH | A. SENSOR GROUND OPEN CIRCUIT B. SENSOR SIGNAL SHORTED TO SENSOR SUPPLY C. SENSOR SIGNAL SHORTED TO BATTERY D. SENSOR FAILURE E. FUNCTIONAL FAILURE IN CONTROLLER |
523780-3 | Park Brake Position Sensor OORH | |
524245-3 | Seat Occupancy Position Sensor OORH | |
521-4 | Brake Pedal Position Sensor OORL | A. SENSOR SUPPLY OPEN CIRCUIT B. SENSOR SIGNAL OPEN CIRCUIT C. SENSOR SIGNAL SHORTED TO SENSOR GROUND D. SENSOR SIGNAL SHORTED TO FRAME GROUND E. SENSOR FAILURE F. FUNCTIONAL FAILURE IN CONTROLLER |
523780-4 | Park Brake Position Sensor OORL | |
524245-4 | Operator Presence System Sensor OORL | |
523833-3 | Glow Plug Relay Driver Output OORH | A. COIL DRIVER OUTPUT SHORTED TO BATTERY. B. FUNCTIONAL FAILURE IN CONTROLLER. |
524195-3 | Cold Start Relay Driver Output OORH | |
523833-4 | Glow Plug Relay Driver Output OORL | A. COIL DRIVER OUTPUT SHORTED TO GROUND. B. FUNCTIONAL FAILURE IN CONTROLLER. |
524195-4 | Cold Start Relay Driver Output OORL | |
1079-31 | 5VE1 & 5VE2 Simultaneously OORH | A. 5 VOLT «E1» SUPPLY SHORTED TO SYSTEM SUPPLY SOURCE B. 5 VOLT «E2» SUPPLY SHORTED TO SYSTEM SUPPLY SOURCE C. 5VOLT E1 AND E2 SIMULTANEOUSLY SHORTED TO SYSTEM SUPPLY SOURCE D. FUNCTIONAL FAILURE IN CONTROLLER |
524260-3 | 5VE2 Sensor Supply Circuit Voltage OORH | |
524261-3 | 5VE1 Sensor Supply Circuit Voltage OORH | |
96-3 | Fuel Level Sensor OORH | A. SENSOR SIGNAL SHORTED TO BATTERY B. SENSOR SIGNAL/RETURN OPEN CIRCUIT C. SENSOR SIGNAL SHORTED TO GROUND D. SENSOR FAILURE |
96-4 | Fuel Level Sensor OORL | |
523833-3 | Glow Plug Relay Driver Output OORH | A. COIL DRIVER OUTPUT SHORTED TO SYSTEM VOLTAGE B. COIL SHORT CIRCUIT C. FUNCTIONAL FAILURE IN CONTROLLER |
523920-3 | REV Circuit Shorted High | |
523930-3 | FWD Circuit Shorted High | |
524195-3 | Cold Start Relay Driver Output OORH | |
524269-3 | Transmission Enable Valve Coil Driver Output OORH | |
523920-4 | REV Circuit Shorted Low | A. COIL DRIVER OUTPUT SHORTED TO GROUND B. COIL/WIRING OPEN CIRCUIT C. FUNCTIONAL FAILURE IN CONTROLLER |
523930-4 | FWD Circuit Shorted Low | |
524269-4 | Transmission Enable Valve Coil Driver Output OORL | |
522606-10 | Post Catalytic Converter Oxygen (O2) Sensor (Slow Response) | A. OXYGEN (O2) SENSOR FAILURE B. FUNCTIONAL FAILURE IN CONTROLLER |
522737-10 | Pre Catalytic Converter Oxygen (O2) Sensor (Slow Response) | |
2000-12 | CAN Tx Failure | A. OPEN/INTERMITTENT CIRCUIT ON CAN HI, CAN LO B. CAN HI AND CAN LO SHORTED TOGETHER C. OPEN CIRCUIT ON POWER/GROUND TO CAN CONNECTED DEVICES D. STG ON CAN HI E. STS/STB ON CAN LO F. CAN CONNECTED DEVICE FAILURE |
2000-12 | CAN Rx Failure | |
2000-14 | CANbus Address Conflict Failure | |
522593-12 | DTC 522593-12 — CANbus Communication Loss — ECU to EPR | |
524233-14 | DTC 524233-14 — Boost Test Override | A. DISPLAY INTERNAL FAILURE |
524234-14 | DTC 524234-14 — Internal Processing Error | |
524236-XX | DTC 524236-XX — Boost Test Failure | |
190-2 | DTC 190-2 — Engine RPM Sensor Output Is Less Than Engine Speed | A. OPEN CIRCUIT IN SENSOR SUPPLY B. SENSOR SIGNAL OPEN CIRCUIT OR SHORT TO GROUND C. SENSOR SIGNAL SHORTED TO BATTERY SOURCE D. SENSOR FAILURE E. FUNCTIONAL FAILURE IN CONTROLLER |
190-7 | DTC 190-7 — Engine Speed Exceeds Command | |
522120-1 | DTC 522120-1 — Engine RPM Higher than XMSN Limit | |
522585-2 | DTC 522585-2 — Engine RPM Sensor (Mazda Gas ECU) | |
523740-3 | DTC 523740-3 — Truck has NO Forward or Reverse Motion | A. HIGH EXTERNAL MAGNETIC FIELDS B. DIRECTIONAL LEVER MECHANISM/MAGNETIC FAILURE C. DISPLAY SWITCH CLUSTER (DSC) FAILURE |
523740-4 | DTC 523740-4 — Truck has NO Forward or Reverse Motion | |
524255-3 | DTC 524255-3 — DSC Temperature OORH | A. DISPLAY SWITCH CLUSTER (DSC) IS OVERHEATED |
524255-4 | DTC 524255-4 — DSC Temperature OORL | |
524255-3 | DTC 524255-3 — DSC Temperature OORH | A. DISPLAY SWITCH CLUSTER (DSC) IS OVERHEATED |
524255-4 | DTC 524255-4 — DSC Temperature OORL | |
524255-3 | DTC 524255-3 — DSC Temperature OORH | A. DISPLAY SWITCH CLUSTER (DSC) IS OVERHEATED |
524255-4 | DTC 524255-4 — DSC Temperature OORL | |
522655-0 | DTC 522655-0 — Short Term Closed Loop Correction Bank 1 Less Than NOR -35% (Rich Engine Operation) | A. PROBLEMS THAT MAY CAUSE LEAN ENGINE OPERATION B. PROBLEMS THAT MAY CAUSE RICH ENGINE OPERATION C. SENSOR FAILURE D. FUNCTIONAL FAILURE IN CONTROLLER |
522655-1 | DTC 522655-1 — Short Term Closed Loop Correction Bank 1 Greater Than NOR 35% (Lean Engine Operation) | |
522660-0 | DTC 522660-0 — Long Term Closed Loop Correction Bank 1 Less Than NOR -30% (Rich Engine Operation) | |
522660-1 | DTC 522660-1 — Long Term Closed Loop Correction Bank 1 Greater Than NOR 30% (Lean Engine Operation) | |
523767-2 | DTC 523767-2 — DSC Fault — Arrow Down Button Stuck | A. BUTTON FAILURE |
523769-2 | DTC 523769-2 — DSC Fault — Arrow Up Button Stuck | |
524206-2 | DTC 524206-2 — DSC Fault — Rear Worklight Button Stuck | |
524208-2 | DTC 524208-2 — DSC Fault — Front Worklight Button Stuck | |
524209-2 | DTC 524209-2 — DSC Fault — Hourmeter Button Stuck | |
190-2 | DTC 190-2 — Crank Loss (CAM Pulse without Crank Pulse) | A. DUST/DEBRIS IN SENSOR HOUSING B. TIMING BELT NOT TENSIONED PROPERLY C. SENSOR OPEN CIRCUIT GROUND/OPEN CIRCUIT SUPPLY D. SENSOR OPEN CIRCUIT SIGNALS E. SENSOR SHORTED CIRCUIT SIGNALS F. SENSOR FAILURE G. FUNCTIONAL FAILURE IN CONTROLLER |
190-4 | DTC 190-4 — Crank Loss (CAM Pulse without Crank Pulse) | |
190-8 | DTC 190-8 — Crank/CAM Synchronization | |
522752-2 | DTC 522752-2 — Crank Loss (CAM Pulse without Crank Pulse) | |
522752-4 | DTC 522752-4 — CAM Loss (Crank Pulse without CAM Pulse) | |
522595-12 | DTC 522595-12 — Internal Circuity Fault Detection | A. EPR FAILURE |
522596-12 | DTC 522596-12 — Internal Circuity Fault Detection | |
524266-31 | DTC 524266-31 — Electronic Throttle Motor/Motor Connections — Short Circuit | A. CONNECTION SHORT CIRCUIT B. ETB MOTOR SHORT CIRCUIT C. ECU/ETB DRIVER FAILURE |
524286-31 | DTC 524286-31 — ECU — ETB Driver Component Failure | |
94-0 | DTC 94-0 — Primary Fuel Pressure Higher Than Expected | A. FUEL PRESSURE SENSOR WIRING FAULT B. FUEL PRESSURE FAULT C. FAULTY CONTROLLER |
94-1 | DTC 94-1 — Primary Fuel Pressure Lower Than Expected | |
520260-3 | DTC 520260-3 — Electronic Pressure Regulator (EPR) OORH | A. DEPR WIRING FAULT B. DEPR FAULT |
520260-4 | DTC 520260-4 — Electronic Pressure Regulator (EPR) OORL | |
91-2 | DTC 91-2 Sensor Signals A and B Not Tracking Correctly | A. DIFFERENCE BETWEEN SENSORS IS BEYOND ALLOWABLE TOLERANCE B. SENSOR FAILURE C. FUNCTIONAL FAILURE IN CONTROLLER |
515-0 | DTC 515-0 RPM Greater Than Throttle Command | A. LARGE LEAKS IN MANIFOLD B. ELECTRONIC THROTTLE ASSEMBLY (ETA) MECHANICAL ISSUES C. FUNCTIONAL FAILURE IN CONTROLLER |
522764-6 | DTC 522764-6 Ign/Alt — Ignition 1 Relay (RL6) Driver Output OORL | A. SHORTED RELAY COIL B. SHORT TO GROUND ON PDM RELAY DRIVER OUTPUT C. FUNCTIONAL FAILURE IN DISPLAY (DSC) |
168-0 | DTC 168-0 System Battery Voltage OORH | A. BATTERY FAILURE B. ALTERNATOR FAILURE C. FUNCTIONAL FAILURE IN CONTROLLER |
168-1 | DTC 168-1 System Battery Voltage OORL | A. BLOWN FUSE OR FAULTY WIRING HARNESS B. IGNITION WIRE FAILURE C. BATTERY FAILURE D. ALTERNATOR FAILURE E. OPERATION CYCLE TOO SHORT TO CHARGE BATTERY F. QUIESCENT CURRENT DRAW TOO HIGH DURING TRUCK OFF TIME |
522697-12 | DTC 522697-12 Internal Central Processor or Circuitry Faults | A. FUNCTIONAL FAILURE IN ECU CONTROLLER |
108-1 | DTC 108-1 Barometric Pressure Below Acceptable Limit | A. OPEN CIRCUIT SENSOR SUPPLY B. SHORTED SIGNAL CIRCUIT TO BATTERY/SENSOR SUPPLY – SIGNAL OPEN CIRCUIT C. SENSOR FAILURE D. FUNCTIONAL FAILURE IN CONTROLLER |
523550-3 | DTC 523550-3 Start Relay Control OORH | A. HARNESS/PDM SHORT CIRCUIT TO SWITCHED OR UNSWITCHED BATTERY B. FUNCTIONAL FAILURE IN CONTROLLER |
522604-3 | DTC 522604-3 Fuel Run Relay Control OORH | A. HARNESS/PDM SHORT CIRCUIT TO SWITCHED OR UNSWITCHED BATTERY B. FUNCTIONAL FAILURE IN CONTROLLER |
522604-4 | DTC 522604-4 Fuel Relay PWM Control OORL | A. OPEN CIRCUIT B. HARNESS/PDM SHORT TO GROUND C. FUNCTIONAL FAILURE IN CONTROLLER |
522604-5 | DTC 522604-5 Fuel Relay not Functioning | A. HARNESS RELAY COIL OPEN CIRCUIT B. FUNCTIONAL FAILURE IN CONTROLLER |
522598-3 | DTC 522598-3 LPG Lock Off OORH | A. COIL TO ECU HARNESS SHORTED TO UNSWITCHED OR SWITCH BATTERY B. COIL SHORTED TURNS C. FUNCTIONAL FAILURE IN CONTROLLER |
522598-4 | DTC 522598-4 LPG Lock Off OORL | A. COIL TO ECU HARNESS OPEN CIRCUIT B. COIL TO ECU HARNESS SHORT TO GROUND C. COIL OPEN CIRCUIT D. COIL SUPPLY OPEN CIRCUIT E. FUNCTIONAL FAILURE IN CONTROLLER |
522592-0 | EPR Pressure Greater Than Commanded | A. WORN OR DAMAGED PRIMARY OR SECONDARY SEAT B. FAULTY ELECTRONIC PRESSURE REGULATOR (EPR) ELECTRICAL CONNECTIONS C. EPR FAILURE |
522592-1 | EPR Pressure Less Than Commanded | A. LOW SECONDARY FUEL PRESSURE DUE TO A FUEL RESTRICTION B. FAULTY ELECTRONIC PRESSURE REGULATOR (EPR) ELECTRICAL CONNECTIONS C. EPR FAILURE |
524227-3 | Manual Hydraulic Lockout Coil OORH | A. COIL DRIVER OUTPUT SHORTED TO BATTERY B. COIL SHORT C. FUNCTIONAL FAILURE IN CONTROLLER |
524227-4 | Manual Hydraulic Lockout Coil OORL | A. COIL DRIVER OUTPUT SHORTED TO GROUND B. WIRING/COIL OPEN CIRCUIT C. FUNCTIONAL FAILURE IN CONTROLLER |
1239-7 | Fuel Run-Out Longer Than Expected | A. LOCK-OFF SOLENOID WIRING FAULT B. LOCK-OFF SOLENOID FAULT C. FAULTY CONTROLLER |
524230-3 | Rear Work Lights Relay (RL7) Driver Output OORH | A. SAFETY SWITCH (IF EQUIPPED) IS DISCONNECTED B. SHORT ON RELAY DRIVER OUTPUT TO UNSWITCHED BATTERY (SEE WARNING BEFORE CONTINUING) C. SHORT ON RELAY DRIVER OUTPUT TO SWITCHED BATTERY. D. SHORT ON RELAY DRIVER OUTPUT TO ANOTHER OPERATED DEVICE E. CONTROLLER DRIVER OUTPUT TO RELAY COIL OPEN CIRCUIT F. RELAY COIL OR GROUND CONNECTION OPEN CIRCUIT G. FUNCTIONAL FAILURE IN CONTROLLER |
524230-4 | Rear Work Lights Relay (RL7) Driver Output OORL | A. SHORTED RELAY COIL B. SHORT TO GROUND ON PDM RELAY DRIVER OUTPUT C. FUNCTIONAL FAILURE IN CONTROLLER |
522631-2 | Pre-Cat Bank 1 Sensor Fails To Switch To Rich | |
522762-4 | Switched Battery Voltage 3 (IGN 3) OORL | A. IGN 1 OR IGN 3 VOLTAGE OUTPUT OPEN SUPPLY B. IGN 2 VOLTAGE OUTPUT SHORTED TO GROUND C. IGN 1 OR IGN 3 OUTPUT SHORTED TO GROUND D. FUNCTIONAL FAILURE IN CONTROLLER |
522772-4 | Backup Lamp Driver Output OORL | A. LAMP DRIVER OUTPUT SHORTED TO GROUND B. FUNCTIONAL FAILURE IN CONTROLLER |
880-4 | Stop Lamp Driver Output OORL | A. LAMP DRIVER OUTPUT SHORTED TO GROUND B. FUNCTIONAL FAILURE IN CONTROLLER |
522760-4 | Switched Battery Voltage 1 (IGN 1) OORL | A. IGN 1 OR IGN 3 VOLTAGE OUTPUT OPEN SUPPLY B. IGN 2 VOLTAGE OUTPUT SHORTED TO GROUND C. IGN 1 OR IGN 3 OUTPUT SHORTED TO GROUND D. FUNCTIONAL FAILURE IN CONTROLLER |
524260-1 | 5 Volt Supply Circuit B OORL | A. 5 VOLT «A» SHORTED TO GROUND B. 5 VOLT «B» SHORTED TO GROUND C. 5 VOLT «C» SHORTED TO GROUND D. VSM FAILURE E. 5 VOLT ECU POWER SUPPLY SHORTED TO GROUND |
522614-7 | Throttle Not at Limp Mode Position (GM Engines Only) | A. MECHANISM STICKY COMPONENT OPERATIONAL CHECK PROCEDURE OR ACTION: 1. Turn power to OFF for no less than 30 seconds, and then to ON to clear displayed DTC. Does reported DTC to reoccur? YES: Go to Step 2. NO: Problem not verified. Resume operation. 2. Conduct a quick visual inspection of all connectors/wiring associated with the displayed fault code. Are any faults detected/observed? YES: Repair/replace connector or wiring associated with faults found. See Electrical System 2200 SRM 1142. NO: Go to Cause A. CAUSE A — MECHANISM STICKY PROCEDURE OR ACTION: 1. Turn truck power ON and start engine. 2. Check for proper operation of the throttle body and the ECU mechanism by exercising the accelerator pedal with the vehicle in neutral. For GM 2.4L gasoline and LPG engines, the engine should idle at 775 to 825 rpm with no pedal and continuing to the governor speed which should be 2675 to 2725 rpm at full pedal. For GM 4.3L gasoline and LPG engines the engine should idle at 725 to 775 rpm with no pedal and continuing to the governor speed which should be 2375 to 2425 rpm at maximum full pedal. Is the throttle mechanism operating smoothly/tracking with accelerator operation? YES: Problem corrected. Resume operation. NO: Ensure truck power is OFF. Clean any fuel residue from mechanism and go to Step 3. 3. Check for proper operation of the throttle body and the ECU mechanism by exercising the accelerator pedal with the vehicle in neutral. For GM 2.4L gasoline and LPG engines, the engine should idle at 775 to 825 rpm with no pedal and continuing to the governor speed which should be 2675 to 2725 rpm at full pedal. For GM 4.3L gasoline and LPG engines the engine should idle at 725 to 775 rpm with no pedal and continuing to the governor speed which should be 2375 to 2425 rpm at maximum full pedal. Is the throttle mechanism operating smoothly/tracking with accelerator operation? YES: Problem corrected. Resume operation. NO: Ensure truck power is OFF. Replace Electronic Throttle Body. For GM 2.4L Gasoline engines see Gasoline Fuel System, GM 2.4L Engine 900 SRM 1126. For GM 2.4L LPG engines see LPG Fuel System, GM 2.4L Engine 900 SRM 1124. For GM 4.3L Gasoline engine see Gasoline Fuel System, GM 4.3L Engine With GFI 900 SRM 1244. For GM 4.3L LPG engine see LPG Fuel System, GM 4.3L Engine With GFI 900 SRM 1242. |
522616-8 | Throttle Not at Command Position (GM Engines Only) | |
522617-5 | Throttle Not at Fully Closed/Open Position (GM Engines Only) | |
522760-3 | Switched Battery Voltage 1 (IGN 1) OORH | A. IGN VOLTAGE SHORTED TO UNSWITCHED BATTERY SOURCE IN PDM OR PDM/VSM HARNESS B. IGN VOLTAGE SHORTED TO UNSWITCHED BATTERY SOURCE IN PDM OUTPUT HARNESS C. IGN VOLTAGE SHORTED TO SWITCHED BATTERY SOURCE IN PDM OR PDM/VSM HARNESS D. IGN 2 VOLTAGE SHORTED TO BATTERY SOURCE E. FUNCTIONAL FAILURE IN CONTROLLER |
135-16 | Fuel Air Pressure minus (MAP) OORH (GM LPG Only) or and Fuel Absolute Pressure Minus (MAP) Too High | |
524240-4 | Washer Pump Drive Command OORL | windshield wiper pump |
522125-8 | Transmission Range1 Valve Current Out Of Range (TCU) | A. HIGH RESISTIVE CONNECTION B. VALVE -VE SHORTED TO BATTERY – VE/FRAME GROUND C. FUNCTIONAL FAILURE IN CONTROLLER |
676-3 | Glow Plug Relay Driver Output OORH | A. RELAY/COIL DRIVER OUTPUT SHORTED TO BATTERY B. RELAY/COIL DRIVER OUTPUT OPEN CIRCUIT C. RELAY/COIL DRIVER RETURN OPEN CIRCUIT D. FUNCTIONAL FAILURE IN CONTROLLER |
524223-4 | Transmission Reverse Pressure OORL | A. SENSOR SUPPLY OPEN CIRCUIT B. SENSOR SIGNAL OPEN CIRCUIT C. SENSOR SIGNAL SHORTED TO SENSOR GROUND D. SENSOR SIGNAL SHORTED TO FRAME GROUND E. SENSOR FAILURE F. FUNCTIONAL FAILURE IN CONTROLLER |
100-4 | Engine Oil Pressure OORL | A. SENSOR SUPPLY OPEN CIRCUIT B. SENSOR SIGNAL OPEN CIRCUIT C. SENSOR SIGNAL SHORTED TO SENSOR GROUND D. SENSOR SIGNAL SHORTED TO FRAME GROUND E. SENSOR FAILURE F. FUNCTIONAL FAILURE IN CONTROLLER |
524224-0 | XMSN Forward 2 Pressure Greater Than Commanded Pressure | A. SENSOR SUPPLY OPEN CIRCUIT B. SENSOR FAILURE C. FUNCTIONAL FAILURE — MECHANICAL |
168-4 | System Battery Voltage OORL | A. BATTERY FAILURE B. ALTERNATOR FAILURE C. OPERATION CYCLE TOO SHORT TO CHARGE BATTERY D. QUIESCENT CURRENT DRAW TOO HIGH DURING TRUCK OFF TIME |
654-5 | GM Gas Drive Injector 4 Open or Circuit Cummins-Code 332. See QSB 3.3L Troubleshooting and Repair | A. FUEL INJECTOR OPEN CIRCUIT B. INJECTOR DRIVER MODULE FAILURE C. FUNCTIONAL FAILURE IN CONTROLLER |
524263-1 | Uncommanded Power Down | A. TCU PROGRAM CORRUPTED OR TCU APPLICATION FILE MISMATCH B. FUNCTIONAL FAILURE IN CONTROLLER |
651-5 | GM Gas Drive Injector 1 Open Circuit,or Cummins-Code 322. See QSB 3.3L Troubleshooting and Repair | A. FUEL INJECTOR OPEN CIRCUIT B. INJECTOR DRIVER MODULE FAILURE C. FUNCTIONAL FAILURE IN CONTROLLER |
652-5 | GM Gas Drive Injector 2 Open Circuit | A. FUEL INJECTOR OPEN CIRCUIT B. INJECTOR DRIVER MODULE FAILURE C. FUNCTIONAL FAILURE IN CONTROLLER |
653-5 | Cummins-Code 324. See QSB 3.3L Troubleshooting and Repair | A. FUEL INJECTOR OPEN CIRCUIT B. INJECTOR DRIVER MODULE FAILURE C. FUNCTIONAL FAILURE IN CONTROLLER |
655-5 | GM Gas Drive Injector 5 Open Circuit | A. FUEL INJECTOR OPEN CIRCUIT B. INJECTOR DRIVER MODULE FAILURE C. FUNCTIONAL FAILURE IN CONTROLLER |
656-5 | GM Gas Drive Injector 6 Open Circuit | A. FUEL INJECTOR OPEN CIRCUIT B. INJECTOR DRIVER MODULE FAILURE C. FUNCTIONAL FAILURE IN CONTROLLER |
2023-12 | CANbus Error With Display | A. TERMINATION RESISTOR(S) OPEN CIRCUIT B. OPEN/INTERMITTENT CIRCUIT ON CAN HI, CAN LO C. CAN HI AND CAN LO SHORTED TOGETHER D. OPEN CIRCUIT ON POWER/GROUND TO CAN CONNECTED DEVICES E. STG ON CAN HI F. STS/STB ON CAN LO G. CAN CONNECTED DEVICE FAILURE |
Share This Story, Choose Your Platform!
Related Posts
Page load link
Go to Top
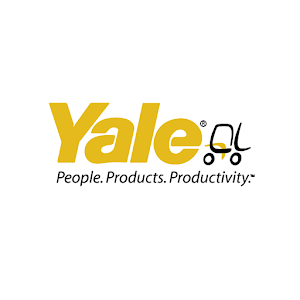
YALE Pallet Lift Truck Fault Codes DTC
Error: no LEDs or LCDs on
What the issue is: Inoperative
Cause of Problem: B+ and / or B- missing at controller, defective battery charger, or defective battery charger
What to do: Ensure the battery is connected, the key switch is on, and the brake override circuit is in the run position; also test your battery charger and motor controller and replace any
nonworking parts
Error: no LEDs or LCDs on
What the issue is: Forklift functions as normal
Cause of Problem: open connection between display and controller, defective display, or defective LEDs
What to do: make sure harnesses are connected at MDI and connector B on controller; test the dash display by connecting a handset to it and testing for communication; test LEDs by disconnecting
them, connecting the handset, and testing the handset; replace any non-working parts
Error: no LEDs or LCDs on
What the issue is: Forklift functions as normal
Cause of Problem: Because this condition is similar to the last, it will take a handset to determine its cause. If the handset displays “NO COMMUNICATION,” the controller is defective.
What to do: replace controller
Error: no alarm
What the issue is: Traction and hydraulic functions not working
Cause of Problem: improper startup sequence by jack operator
What to do: check brake switch, accelerator, steer handle, and hydraulic inputs
Error: AL66
What the issue is: Hydraulic function not working
Cause of Problem: battery voltage is low or controller voltage calibration is incorrect
What to do: Charge or replace battery; otherwise, use handset to determine the voltage read by the controller and compare it to an actual voltmeter reading; replace controller if the two readings
differ by more than 1.5 volts
Error: AL99
What the issue is: Traction and hydraulic functions not working
Cause of Problem: incorrect battery selected, damaged battery, or damaged connection to batter
What to do: check that you have the right voltage for your truck, manually check the voltage of your battery, inspect it for any damage, and check its connecting crimps and cables for damage as
well
Error: AL01
What the issue is: Traction and hoist functions not working
Cause of Problem: control card throttle or lift/lower calibration is out of range; control card is damaged or defective
What to do: Use the tester function on a handset to see if either calibration is greater than 1 volt at neutral; replace control card if damaged or defective, which can be checked by seeing if
both “forward switch” and “backward switch” are on at the same time when testing
Error: AL01
What the issue is: Traction and hoist functions not working
Cause of Problem: incomplete connection between control card and controller; traction reversing switch not connected; damaged or defective tiller card
What to do: Check connections between control card and controller; use a handset to test for operation of traction reversing switch; replace control card if tiller card is damaged
Error: AL02
What the issue is: Traction and hydraulic functions not working
Cause of Problem: main contactor tips are welded closed or motor field circuit is broken
What to do: disconnect power leads at contactor and test for an open circuit; check connections between motor field and controller
Error: AL04
What the issue is: traction and hydraulic functions not working
Cause of Problem: damaged connection to lowering valve; damaged lowering coil or lowering valve cartridge
What to do: check electrical connection between valve coil and controller; check lowering valve coil for resistance, replace if not approximately 17.7 ohms; replace lowering valve cartridge if
necessary
Error: AL05
What the issue is: traction and hydraulic functions not working
Cause: damaged connection to brake or brake coil damaged
What to do: check connection between electric brake and controller; check brake coil for resistance in both directions and replace if not between 27.36 and 30.24 ohms
Error: AL06
What the issue is: Traction and hydraulic functions not working
Cause of Problem: Damaged connection to traction motor; traction motor armature resistance is too low; field wires are loose or damaged; motor field winding is shorted or too low.
What to Do: Check electrical connection between traction motor, field wires, and controller; check traction motor armature for shorts; check motor field resistance and correct if not between 0.5
and 1.5 ohms; check contactor coil for resistance of 52 ohms
Error: AL07
What the issue is: traction functions reduced below 14°F or above 167°F and not working above 194°F
Cause of Problem: controller temperature is too hot or cold; controller temperature is not calibrated correctly; controller sensor or controller itself is damaged
What to do: move truck to a warmer or cooler location; use a handset to check that controller temperature matches room temperature (if not, replace controller)
Error: AL8
What the issue is: traction and hydraulic functions not working
Cause of Problem: over current in driven component
What to do: check main harness for damaged connections to main contactor, brake, and electric valve coils; check contactor, brake, and electric valve coils for correct resistance (52 ohms for
contactor, between 27.36 and 30.24 ohms for brake coil, and 17.7 ohms for electric valve coils)
Error: AL10
What the issue is: Traction and hydraulic functions not working
Cause of Problem: controller is damaged; damaged wire connection; short circuit in harness; ground between motor windings and chassis; motor field winding is shorted to chassis; field current
driver circuit has failed; watchdog hardware circuit is damaged
What to do: Cycle key switch off and on and replace controller if problem not solved; check wire connections at contactor, pump motor, and traction motor; check main harness for shorts; check for
grounds or shorts between motor windings and chassis; check motor field resistance (should be about 1.5 ohms); measure voltage between F1 and B- and F2 and B- on field current driver (should be
half the voltage between B+ and B-)
Error: AL94
What the issue is: Traction and hydraulic functions not working for one minute.
Cause of Problem: No fault is occurring. The controller is installing hour meter memory from MDI display if controller has been replaced.
What to do: No solution necessary. Fork truck will operate as soon as data transfer is complete.
Title |
File Size |
Download Link |
YALE B974 GDP25LX LIFT TRUCK Service Repair Manual.pdf |
3.4Mb |
Download |
Yale Electric Forklift ERC040-065GH (A908), ERC030-040AH (B814), ERP040-060DH(D216) Operating Manual.pdf |
19.2Mb |
Download |
Yale Electric Forklift Maintenance Manual.pdf |
990.7kb |
Download |
Yale Forklift ERC040RG Service Manual.pdf |
7.5Mb |
Download |
Yale Forklift ERC040ZG Service Manual.pdf |
7.5Mb |
Download |
Yale Forklift ERC050RG Service Manual.pdf |
7.5Mb |
Download |
Yale Forklift ERC050ZG Service Manual.pdf |
7.5Mb |
Download |
Yale Forklift ERC060RG Service Manual.pdf |
7.5Mb |
Download |
Yale Forklift ERC060ZG Service Manual.pdf |
7.5Mb |
Download |
Yale Forklift ERC065RG Service Manual.pdf |
7.5Mb |
Download |
Yale Forklift ERC065ZG Service Manual.pdf |
7.5Mb |
Download |
Yale Forklift ERC070HG Service Manual.pdf |
2.2Mb |
Download |
Yale Forklift ERC080HG Service Manual.pdf |
2.2Mb |
Download |
Yale Forklift ERC100HG — 39 Service Manual.pdf |
2.2Mb |
Download |
Yale Forklift ERC100HG — 45 Service Manual.pdf |
2.2Mb |
Download |
Yale Forklift ERC120HG Service Manual.pdf |
2.2Mb |
Download |
Yale Forklift ERP15VT, 16VT, 18VT, 20VT(G807) Parts Manual.pdf |
14.2Mb |
Download |
Yale Forklift GLP050LX, GDP50LX(A974) Parts Manual.pdf |
7.4Mb |
Download |
Yale Forklift GLP050LX(A974) Parts Manual.pdf |
5.4Mb |
Download |
Yale Forklift GLP050TG, GLP060TG, GP050TG, GP060TG Parts Manual.pdf |
9.4Mb |
Download |
Yale Forklift GP-GTP-GDP 050-055-060 RL-TL Parts Manual.pdf |
36.8Mb |
Download |
Yale Forklift GP080-120VX, GLP080-120VX,GDP080-120VX VERACITOR(G813) Parts Manual.pdf |
13.3Mb |
Download |
Yale Forklift Project Report — 1.pdf |
1010.8kb |
Download |
YALE G807 ERP18VT LIFT TRUCK (EUROPE) Service Repair Manual.pdf |
6.3Mb |
Download |
Yale j813gp-glp-gdp110vx lift truck service repair manual.pdf |
2.8Mb |
Download |
Yale Forklift MR 14-20 H,W (C849) Service Manuals
Size: 53.9 MB
Format: PDF
Language: English
Brand: Yale
Type of Vehicle: Forklift
Contents:
Yale Forklift MR 14-20 H,W (C849) 14-20 H,W (C849)
Yale Forklift MR 14-20 H,W (C849) 8804726R0 Software
Yale Forklift MR 14-20 H,W (C849) MR Assemble Manuals
Yale Forklift MR 14-20 H,W (C849) MR 14-20 (C849) _ Online_Bulletins_List
Yale Forklift MR 14-20 H,W (C849) MR 14-20 (C849) _ Softwarelist
Yale Forklift MR 14-20 H,W (C849) MR 14-20 H,W (C849) Parts Manual